Precast concrete panel joint sealant
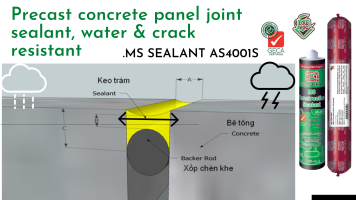
Precast concrete panel joint sealant
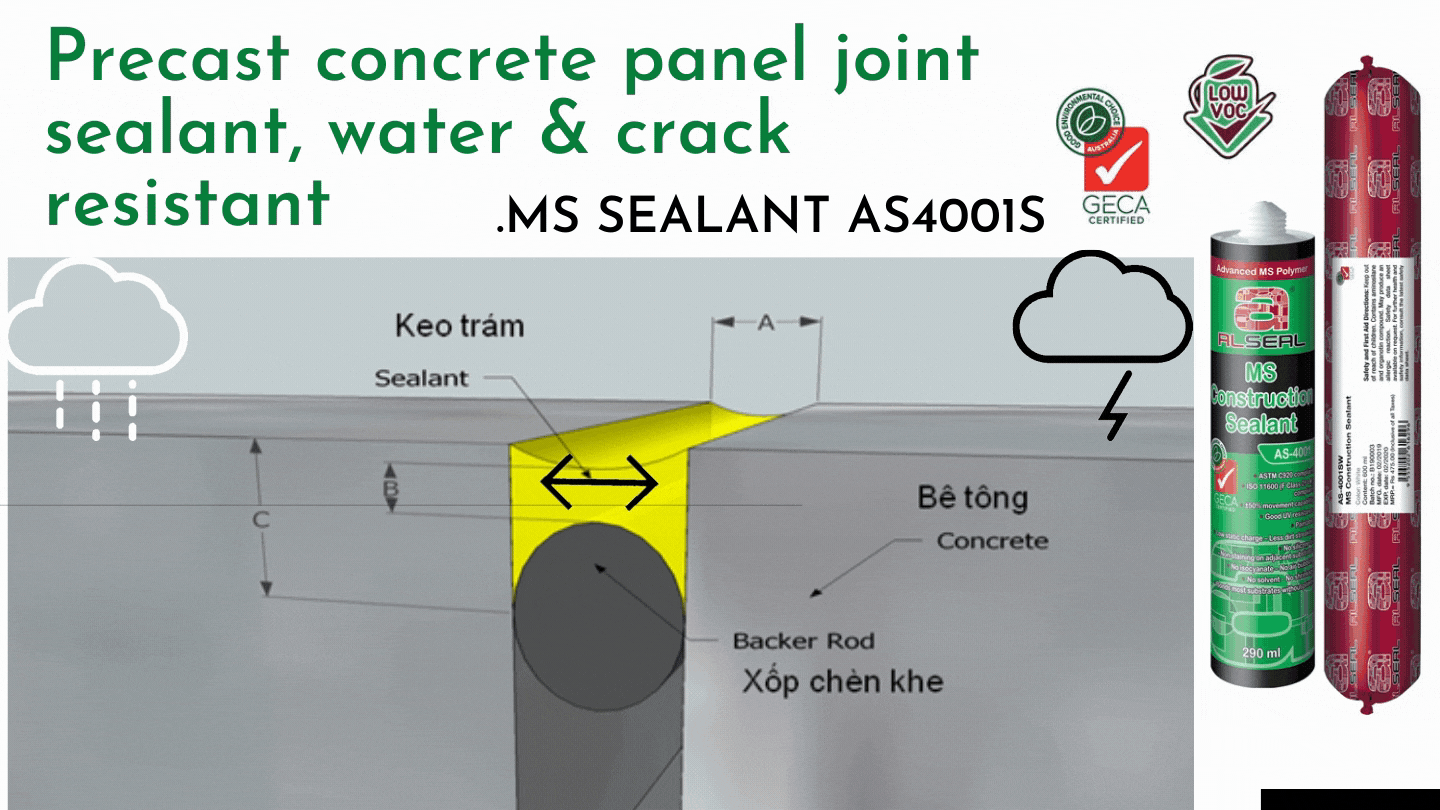
- Standard Guide for Use of Joint Sealants, ASTM C1193-13. ASTM International, 2013.
- Standard Guide for Calculating Movement and Other Effects When Establishing Sealant Joint Width, ASTM C1472-10. ASTM International, 2010.
- Crack Control in Concrete Masonry Walls, TEK 10-1A. National Concrete Masonry Association, 2005.
- Control Joints for Concrete Masonry Walls – Empirical Method, TEK 10-2C. National Concrete Masonry Association, 2010.
- Design for Dry Single-Wythe Concrete Masonry Walls, TEK 19-2B. National Concrete Masonry Association, 2012.
- Standard Specification for Elastomeric Joint Sealants, ASTM C920-11. ASTM International, 2011.