Corrosion in the electric power industry
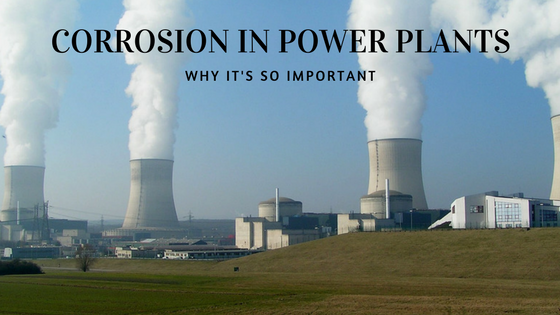
Corrosion, the plant operators’ headache
Corrosion in the electric power industry results in loss of millions of US$ annually. The revelations come at a time when plants are working to enhance efficiency and shorten the offline maintenance timeline. Corrosion prevention techniques can go a long way to improve the life of various machinery components and enhance plant safety.
The most common types of corrosion issues in thermal plants include erosion, oxide corrosion and galvanic corrosion. Erosion arises when an aggressive chemical environment comes into contact with high fluid surface velocities thereby increasing surface wear outside the protective coating or scale area. With oxide corrosion, the electrochemical process arises when metal is exposed to water causing the composition to change. The galvanic corrosion process, on the other hand, occurs when two dissimilar metals come into contact. When that happens, the effect is an electrical reaction that accelerates corrosion. Thermal power plants, whether coal, solar thermal electric, nuclear or geothermal plants operate by generating steam that drives turbines that turnaround electrical generators to produce power. There are several components in the thermal power plants that operate at different temperatures and pressures. These components include cooling tower, boilers, superheater, turbine and steel drums. When any of these components are exposed to corrosion, the system operation may be compromised causing serious safety hazard issues. This is especially true if a worker comes into contact with radioactive materials, gas and hot steam because of leaks or damage. Corrosion can also force the thermal power plant operators to grapple with non-operation delays even after scheduled maintenance is performed or be requested to pay nondelivery fees. Corrosion in thermal power plants can be prevented if the operators take into mind the following preemptive measures.- Ensure the generators operate under low humidity levels using a closed loop system
- Seal the turbine opening to keep it as tight as possible
- Use water conditioning agents to counter the presence of organic agents or chemicals that cause corrosion. The other strategy is replacing the steel components with a line of effective composites.
- Perform regular inspections and test components exposed to the risk of corrosion. The key focus areas include welded areas, ducts, pipes, and turbines.
- Install a windshield or protective liner on the cooling stacks to prevent thermal shock and chemical attacks.
- Install insulation materials with preventive coating or jacket on all vulnerable pipes. Also, consider improving the pipe design to counter corrosion.