Water tank waterproofing | zero span tension elongation and adhesion strength criteria
Water tank waterproofing | The importance of balance of zero span tension elongation and adhesion strength criteria
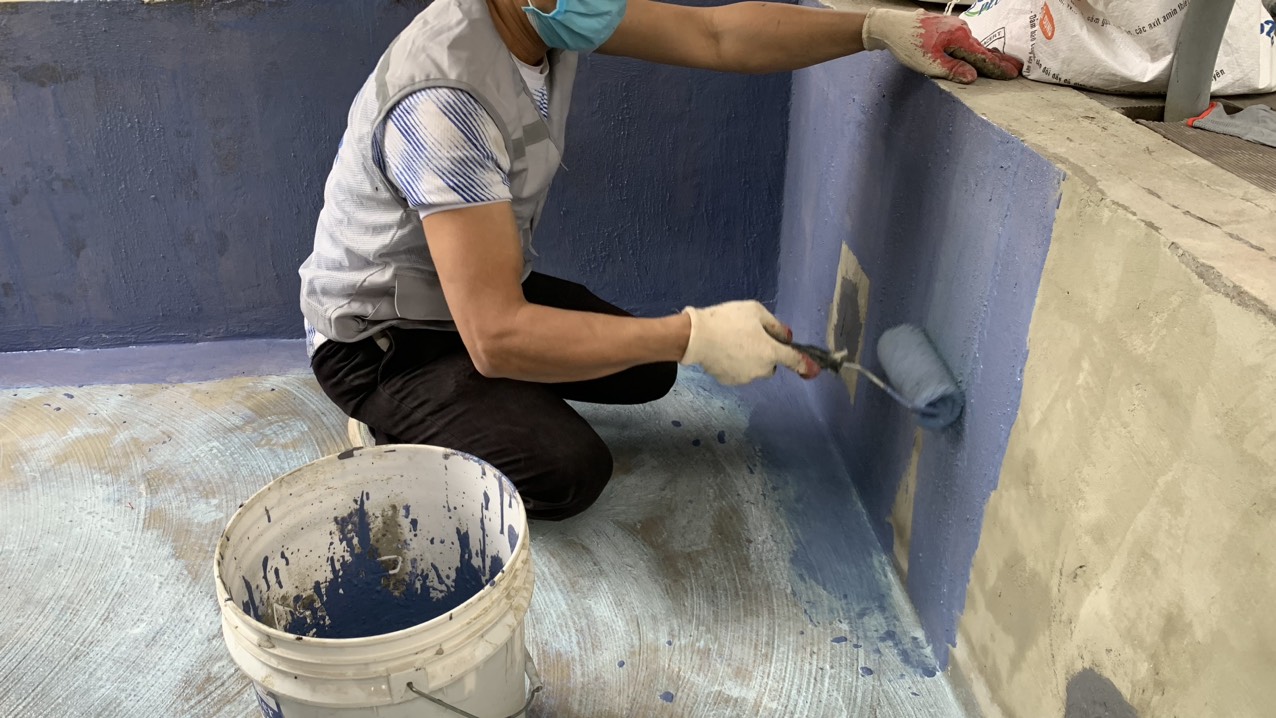
To maintain good waterproof function over long periord of time, waterproofing membrane should have both sufficient zero span tension elongation amount that can follow the cracks generated in the structure, and sufficient adhesion strength too.
Waste water treatment structure such as a waste water storage tank in a sewage facility and a water storage for drinking water. Polymer for waterproofing material suitable for use in a structure that can store liquid in the container, such as a tank, a water receiving tank provided in the basement, a fire extinguishing water tank, etc.
If the structure is a concrete structure, and the structure is a concrete container that stores wastewater or drinking water for a long period of time, the function of the structure will be impaired if the stored liquid flows out of the container. Therefore, it is necessary to waterproof the surface of the structure having such a contact surface with the liquid.
Water storage tank has a longer period of contact with the liquid than the transport pipe of waste water or drinking water or the outer wall of the building, and is continuously in contact with the liquid, so that the waterproof material has particularly high waterproof performance and reliability.
Here, in order for the waterproof material applied to the structure made of concrete to have a high waterproof property, it has a sufficient zero span tension elongation amount that can follow the cracks generated in the structure, and also against the surface of the structure. It is desirable to have sufficient adhesion strength.
Furthermore, in a water tank that is exposed to liquid for a long period of time, it is also important to have a high tensile strength in order to maintain a waterproof function over a long period of time without breaking in a state of following a crack. However, the conventional acrylic polymer cement has a problem that it cannot be said that the tensile strength property is sufficiently high.
Zero span tension elongation refers to a length that allows the waterproof material to follow a crack generated in a structure coated with the waterproof material without breaking. Concrete structures can crack when used for long periods of time. At this time, for example, when the structure is the container of the water storage tank, the liquid stored in the container flows out of the container when the waterproof material is stretched and cracked along with the crack of the container. If the value of the zero span tension elongation of the waterproof material is large, the waterproof material can be stretched following the cracked container without being broken, so that the liquid can be prevented from flowing out. Therefore, the magnitude of the zero span tension elongation amount of the waterproof material is closely related to the waterproof property of the waterproof material. Also, the measurement of the zero span tension elongation amount is performed by causing the base plate to crack in the state where the waterproof material to be measured is applied to the base plate, and is therefore suitable for the actual performance evaluation of the waterproof material.
The zero span tension elongation value has a strong correlation with the elongation rate of the waterproof material. That is, the greater the elongation rate, the larger the waterproof material can be stretched, and therefore it is possible to follow even large cracks. However, it is not sufficient to evaluate the magnitude of the zero span tension elongation amount only by the elongation rate, and it is also necessary to evaluate the tensile strength indicating the mechanical strength of the waterproof material. This is because by having a high tensile strength, the waterproof material is not broken even by a strong force generated when a crack is generated, and the stretched state can be maintained.
On the other hand, when the waterproof material keeps in contact with the liquid stored in the container for a long period of time, a part of the waterproof material is peeled off from the surface of the container and is likely to float or swell. When the waterproof material floats or bulges, the liquid stored in the container enters between the waterproof material and the container, which accelerates the penetration of the liquid into the concrete wall forming the container and the deterioration of the container. Furthermore, the liquid will flow out of the container. If the adhesion strength of the waterproof material is large, it is possible to suppress the occurrence of floating of the waterproof material, and thus it is possible to prevent liquid from leaching into the container and cracking due to deterioration of the container. Accordingly, the adhesion strength of the waterproof material is closely related to the waterproof property of the waterproof material with respect to the prevention of liquid outflow caused by the occurrence of floating and swelling of the waterproof material.
The conventional acrylic polymer cement is used as a waterproof material because of its high elongation and excellent flexibility. Here, in the waterproof material formed by the conventional acrylic polymer cement, the zero span tension elongation amount and the adhesion strength of the waterproof material can be changed by changing the blending ratio of the acrylic resin component weight contained in the acrylic resin emulsion to the cement weight. It was adjusted.
However, in the conventional acrylic polymer cement, when the blending ratio of the acrylic resin to the cement weight is increased, the zero span tension elongation amount of the waterproof material can be increased, but the adhesion strength is decreased. On the other hand, if the blending ratio of the acrylic resin emulsion to the cement weight is decreased, the adhesion strength of the waterproof material can be increased, but the zero span tension elongation amount is decreased. For this reason, it has been difficult to achieve both the zero span tension elongation and adhesion strength of conventional waterproofing materials.
As mentioned above, the adhesion strength of waterproofing materials is also closely related to waterproofness, so finding the zero span tension elongation simply because the crack followability is high is at the expense of the adhesion strength. As a result, there was a problem that it was necessary to make difficult decisions on material design.
A waterproof material designed to have a balanced and high value for all of the zero span tension elongation amount, adhesion strength, and tensile strength, which are important characteristics as a waterproof material, and extremely waterproof to provide this. An excellent polymer cement composition for waterproofing material can be realized.
UBE has conquered the weather and fatigue resistance issues that were the drawbacks of previous polymer-modified cement waterproofing materials, and can now offer waterproofing performance over a long period of time. These next-generation waterproofing materials can meet the various needs for indoor waterproofing.